How AI-Driven Digital Inspections Benefit Building Enclosure Pros
Traditional Versus Digital Building Enclosure Inspections
For building enclosure professionals, precision, efficiency, and documentation accuracy are non-negotiables. Traditionally, inspections involved manual data collection, visual assessments, and written reports—processes prone to human error and time delays. However, with the emergence of AI-driven digital visual inspections, the game is rapidly changing. Building enclosure pros are now leveraging drone-data capture technology to enhance inspection accuracy, streamline workflows, and drive better outcomes for clients.
The Traditional Inspection Bottleneck
Traditional building enclosure inspections typically involve a mix of site walks, note-taking, handheld photography, and later, hours of manual data entry and report writing. Consultants have to juggle multiple file types and ensure all findings are accurately translated into technical reports for stakeholders. These processes are time-consuming, labor-intensive and often result in inconsistent quality.
Moreover, manual inspections may miss early-stage defects or rely heavily on subjective judgments. For example, issues like subtle water infiltration, improper sealing, or thermal bridging can go unnoticed during manual checks, leading to costly failures down the line.
Enter AI-Driven Digital Inspections
AI-driven digital inspection platforms harness the power of computer vision, machine learning, and cloud-based reporting to augment capabilities. These tools use high-resolution imagery, drone data, and smart algorithms to analyze building envelopes for potential failures, defects, and inefficiencies.
A 2023 report by McKinsey & Company found that AI-based inspection tools reduced manual inspection time by 30–50% and improved detection rates of enclosure issues by 40% compared to traditional methods. The implications for building enclosure consultants are significant.
Key Benefits for Building Enclosure Pros
1. Faster & More Accurate Defect Detection
AI algorithms are trained on thousands of images of common enclosure issues—such as cracked sealants, moisture intrusion, and facade delamination—allowing them to detect problems with remarkable accuracy. Tools like Pointivo’s Facade Inspection App automatically flag inconsistencies and highlight areas requiring deeper review.
Use Case: A building consultant in Boston used AI-powered drone imaging to inspect the façade of a 15-story office building. The software flagged several micro-cracks and water ingress points missed during previous manual inspections. As a result, early repairs saved the client an estimated $250,000 in potential water damage.
2. Enhanced Reporting & Documentation
AI-driven digital inspection platforms generate automated reports complete with annotated images, thermal maps, and 3D models or digital twins. This documentation not only reduces report-writing time but also provides clients with visually rich insights.
Use Case: In a recent university building retrofit, AI software created real-time thermal imaging reports. These visuals demonstrated energy leakage points in the roof and curtain wall systems, leading to optimized repair strategies and a 15% reduction in energy costs post-project.
3. Data-Driven Maintenance Planning
One of the most powerful aspects of AI-driven inspections is their ability to predict future problems. Machine learning models can identify patterns that precede enclosure failures—like specific crack propagation patterns or moisture accumulation rates—enabling predictive maintenance.
Use Case: A facility management team at a hospital integrated AI-driven digital inspection software into their yearly assessment schedule. Over time, the system predicted potential flashing failures and helped prioritize maintenance tasks, reducing emergency repairs by 35% over two years.
4. Improved Safety & Accessibility
Inspecting high-rise facades or difficult-to-access roof areas traditionally requires scaffolding or rope access, increasing risk and cost. With AI-powered drones and image recognition, consultants can now inspect dangerous or remote areas from the ground.
Stat: A recent study presented at the IIBEC annual conference found that drone-based inspections cut fall risk exposure by 80% while reducing inspection costs by 25% for high-rise projects.
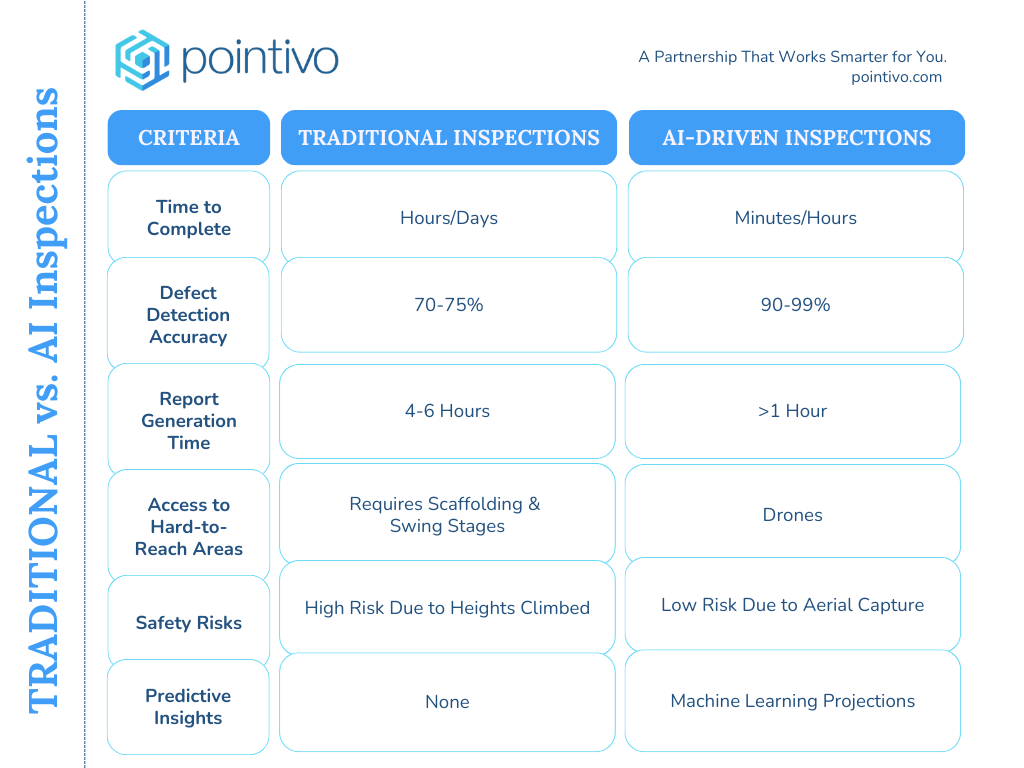
Real-World Adoption and Trends
AI inspection adoption is growing rapidly. According to Dodge Construction Network, over 42% of U.S. construction firms were piloting AI-powered inspection tools in 2024—a figure expected to surpass 60% by 2026. Enclosure consultants are at the forefront of this shift, driven by client demands for faster turnarounds and more accurate insights.
Firms like SGH, Wiss, Janney, Elstner Associates, and Walter P Moore are already integrating AI-driven inspections into their workflows. These companies report faster project cycles, improved client satisfaction, and better risk mitigation—critical in today’s performance-driven building environment.
The Future is Now
AI-driven digital inspections are no longer the future, they’re now. For building enclosure consultants, these tools are not about replacing human expertise but enhancing it. By automating the repetitive, capturing hard-to-see defects, and generating real-time insights, AI is empowering building enclosure pros to deliver better service, reduce liability, and increase the long-term performance of building envelopes.
In an industry where precision meets performance, embracing AI is not just a competitive edge—it’s a professional imperative.
To learn more about Pointivo’s AI-driven platform and reporting capabilities, contact us at team@pointivo.com.
Don’t forget to share this post!
[tags]