Digital Inspections & the Difference Between “As-Designs” & “As-Builts” with Drone Data Capture
Connecting the Interplay with Digital Twins
In construction, engineering, and telecommunications infrastructure, accurate documentation of structures is vital for compliance and operational efficiency. Two terms commonly used in this context are as-designs and as-builts. While they may seem similar at first glance, these concepts serve distinct purposes. Understanding their differences and how they integrate with modern digital inspection methods—particularly drone data capture—can support OPEX efficiency and how organizations manage their assets.
What Are “As-Designs”?
As-designs refer to the original design plans or blueprints created during a project’s planning phase. These documents detail how a structure, such as a telecom tower or a building, is intended to be built.
Key features of as-designs include:
- Specifications: Material requirements, dimensions, and structural details.
- Intent: They represent the theoretical or idealized version of the project.
- Regulatory Compliance: As-designs are often created to meet specific codes and standards.
In essence, as-designs are the “roadmap” for the construction process, offering a clear guide for contractors and engineers.
What Are “As-Builts”?
As-builts, on the other hand, are updated versions of the design documents that reflect the final, built structure. These include any deviations made during the construction process, whether due to site conditions, material availability, or on-the-spot engineering decisions.
Key features of as-builts include:
- Accuracy: They show the exact dimensions, materials, and placements of elements after construction is completed.
- Changes: Notes or annotations highlight deviations from the original as-designs.
- Operational Utility: Used for maintenance, repairs, and future upgrades.
As-builts provide a snapshot of the reality of the structure, as opposed to the theoretical expectations laid out in the as-designs.
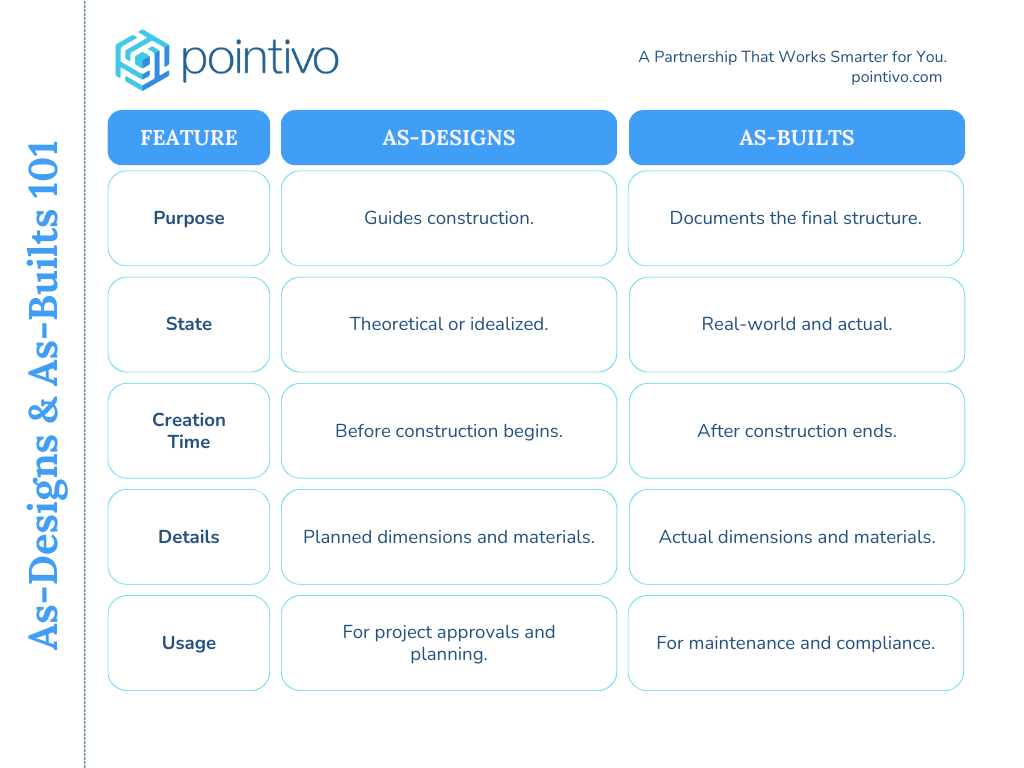
The Role of Drone Data Capture in Digital Inspections
Drone technology has emerged as a powerful tool for capturing data for both as-built documentation and digital inspections. By providing high-resolution imagery, 3D models, and precise measurements, drones bridge the gap between as-designs and as-builts. Here’s how they contribute:
1. Creating Accurate As-Builts
Drones equipped with LiDAR or photogrammetry capabilities can capture detailed visual and spatial data of a structure. This data can be processed into 3D models or digital twins, allowing engineers to compare the actual structure against the original design.
2. Validating As-Designs
During construction, drone inspections can help ensure that the structure is being built according to the as-design specifications. Any discrepancies can be flagged and corrected early, reducing costly rework.
3. Enhancing Compliance & Maintenance
Accurate as-builts created with drone data are invaluable for compliance audits and routine maintenance. For example, telecom towers require regular inspections to ensure they meet safety and performance standards. Drones can quickly capture current conditions and compare them against the as-builts.
4. Streamlining Processes
Traditional as-built documentation often involves manual measurements and photography, which are time-consuming and prone to human error. Drones automate and accelerate this process while providing highly accurate results.
Practical Applications for Commercial Facilities and Properties: Connecting As-Designs and As-Builts
By integrating digital inspections and drone-enabled data capture with as-design and as-built documentation, property managers and engineers gain unprecedented clarity on the alignment between intended designs and real-world conditions.
Here’s how digital inspections enhance various aspects of managing commercial properties, with a focus on the interplay between as-designs and as-builts.
1. Roofing Inspections and Maintenance: Validating Design vs Reality
Challenges in Traditional Inspections:
- Labor-intensive processes requiring scaffolding or ladders.
- Safety risks, especially on complex or elevated structures.
- Difficulty identifying issues in hard-to-reach areas.
Role of As-Designs and As-Builts:
As-designs of roofing layouts specify materials, drainage, and structural elements. Over time, as-builts may reflect modifications made during construction, such as changes in drainage slopes or material substitutions.
Drone-Enabled Digital Inspections:
- Compare drone-captured imagery with as-designs to detect deviations or flaws, like improperly installed components.
- Use thermal imaging to identify pooling or leaks that deviate from the as-built plans.
- Highlight discrepancies that require updates to as-built records.
Practical Benefits:
- Expedites inspection time while ensuring safety.
- Ensures as-builts are accurate for future repairs and compliance audits.
- Prevents long-term damage by identifying misalignments early.
2. Facade and Structural Assessments: Aligning Visuals with As-Builts
Importance for Commercial Properties:
Facades play a critical role in aesthetics and safety. As-designs typically define structural specifications, while as-builts document real-world adjustments, such as materials used or unexpected settling.
Drone-Enabled Inspection Capabilities:
- Capture high-resolution visuals of facades to check alignment with as-built plans.
- Detect issues like cracks or material shifts that weren’t in the original as-designs.
- Create 3D models to overlay drone data on existing as-builts for analysis.
3. HVAC System Monitoring: Tracking Changes from Installation to Operation
The Need for HVAC Inspections:
As-designs outline HVAC placement, duct routes, and airflow patterns, while as-builts document changes during construction due to site-specific constraints.
Drone-Assisted Inspection Benefits:
- Use thermal sensors to validate that as-built ductwork performs as designed.
- Detect inefficiencies, such as energy loss or improper airflow, that diverge from original specifications.
4. Property Surveys and Site Planning: As-Designs Meet Real Terrain
Why Surveys Are Essential:
During property acquisition or expansion, as-designs must align with the actual topography captured in surveys. Drones simplify this comparison.
Drone Survey Capabilities:
- Capture detailed terrain data to verify or update as-designs.
- Create digital twins to overlay site conditions onto as-built layouts.
5. Parking Lot and Outdoor Area Inspections: Checking Layout Accuracy
Challenges in Manual Inspections:
Parking lots often undergo real-world adjustments that deviate from as-designs, such as changes in drainage systems or traffic flow.
Drone Applications:
- Compare drone-captured layouts to as-designs to validate dimensions and features.
- Use thermal imaging to detect subsurface anomalies, like voids or cracks, that differ from as-built documentation.
6. Energy Efficiency and Sustainability Audits: Validating Green Designs
Focus on Sustainability:
As-designs for energy-efficient properties specify insulation and solar installations. As-builts document whether these features were implemented as planned.
Drone-Assisted Inspections:
- Use thermal imaging to identify insulation gaps or inefficiencies.
- Monitor solar panel placements against as-design plans, checking for shading or misalignments.
7. Emergency Response and Post-Disaster Assessments: Rapid Updates to As-Builts
Why It’s Critical:
After disasters, as-builts must be updated to reflect damages or repairs, ensuring future safety and compliance.
Drone Role:
- Survey structures to assess damage against pre-disaster as-builts.
- Document changes made during recovery for updated records.
8. Tenant Space Optimization: Fine-Tuning As-Builts for Utility
Importance for Property Management:
As-designs of tenant spaces often need adaptation to match real-world use, captured in as-builts.
Drone and Digital Tools:
- Use aerial data to analyze space utilization and layout efficiency.
- Update as-builts to reflect changes in tenant needs or property use.
Practical Application: Telecom Tower Inspections
For industries like telecommunications, where tower structures are often complex and located in challenging environments, drone inspections are transformative. Here’s how as-designs, as-builts, and drone data come together:
-
Pre-Construction: As-designs are developed and approved.
-
During Construction: Drones monitor progress, ensuring alignment with as-designs.
-
Post-Construction: Drones capture the final structure to create as-builts.
-
Ongoing Maintenance: Regular drone inspections compare the current state against the as-builts, ensuring that modifications or wear are documented and addressed.
This seamless integration improves safety, reduces costs, and ensures compliance with telecom industry regulations.
Real World Outcomes
A significant example of transitioning from traditional as-built and as-design methods to digital inspections comes from the construction and manufacturing sectors. Companies adopting digital tools, such as Building Information Modeling (BIM) and drone-based inspections, have achieved measurable benefits. For instance:
- One study indicated that construction companies leveraging digital technologies, including drones for site monitoring, reduced rework costs by up to 40%. This translates to substantial savings, as rework costs can contribute to over $31 billion in losses annually across the U.S. construction industry. Digital systems eliminate errors by ensuring that as-built conditions align with as-design specifications in real-time. Source: CRB.
- Firms integrating digital delivery workflows for projects have cut schedules by several weeks or months. This is due to improved collaboration across stakeholders, which prevents the redesign cycles common in siloed, manual processes. Source: CRB.
The interplay between as-designs and as-builts forms the foundation of efficient asset management. Drone technology enhances this relationship by providing accurate, real-time data for digital inspections. As industries continue to adopt drone data capture, the gap between the theoretical and the real will narrow, leading to safer, more efficient, and compliant structures.
Connecting these methods and technologies not only ensures better documentation but also empowers organizations to maintain and upgrade their assets confidently. Whether you’re managing commercial properties, telecom towers, or other infrastructure, leveraging drones for as-built documentation is no longer a luxury—it’s a necessity for modern operations.
To learn more about Pointivo’s AI-driven platform and reporting capabilities, contact us at team@pointivo.com.
Don’t forget to share this post!
[tags]